China is the largest producer and the biggest high-tech CNC (Computer Numerical Control) machine tools consumer worldwide. According to China Machine Tool Industry Association, the output of China’s machine tool industry ranks first in the world, with an output of 19.42 billion USD in 2021, holding a share of 23.1% of the global market.
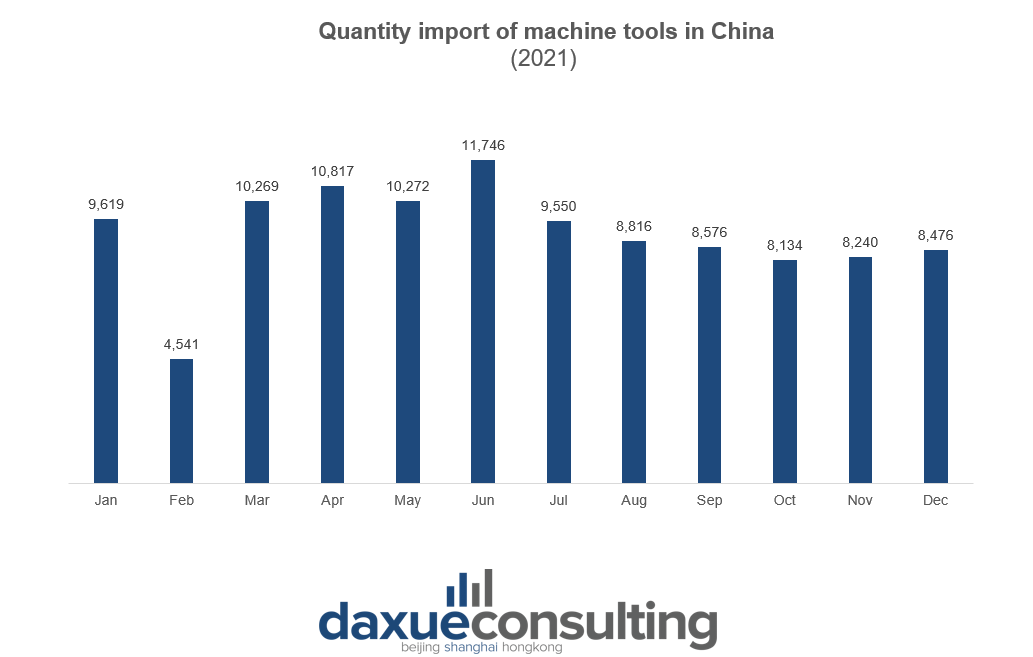
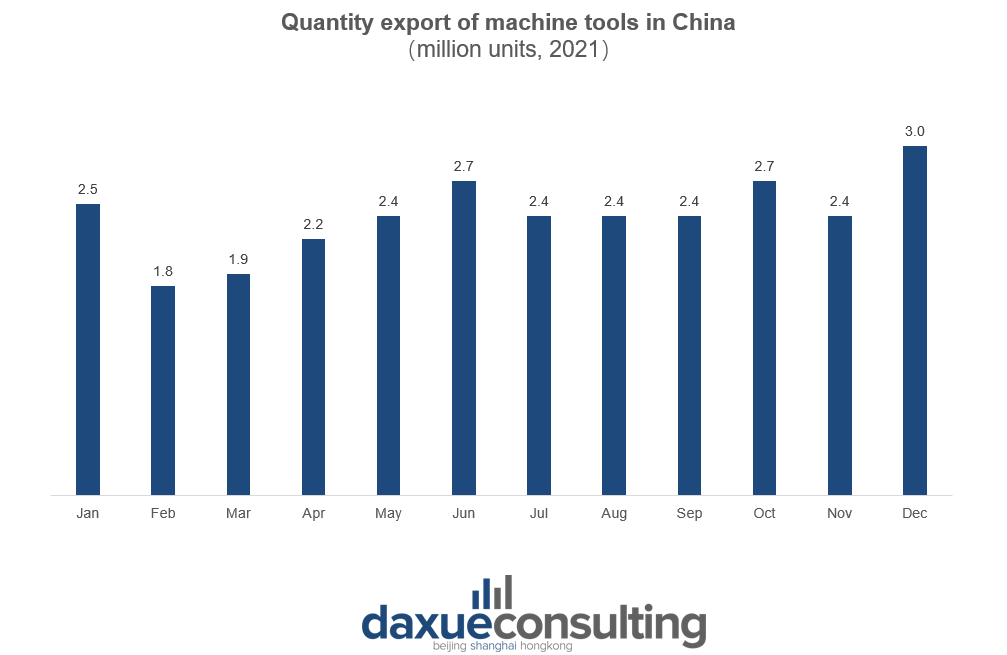
However, the Chinese medium and high-end machine tools industry heavily relies on Asian and European countries exports, and the localisation rate in this segment is lower than 10%. In 2021, the average price of machine tools exports in China was 300 USD / unit, and the number of import prices was 76,700 USD / unit. When it comes to the field of application of domestic low-end CNC machine tools, the automotive sector accounts for a relatively high proportion, accounting for 40%, whereas aerospace, mould and construction machinery industries account for 17%, 13% and 10%, respectively.
Chinese machine tool manufacturers are mainly distributed in eastern, central, and southern China, especially in Jiangsu, Shandong, Zhejiang, Guangdong, and Hebei provinces. China is a large exporter of low-end CNC machine tools, exporting to numerous countries around the world. The main destinations of Chinese exports include Vietnam, the United States, India, and the Russian Federation, accounting for 8.00%, 7.40%, 7.20%, and 6.20%, respectively.
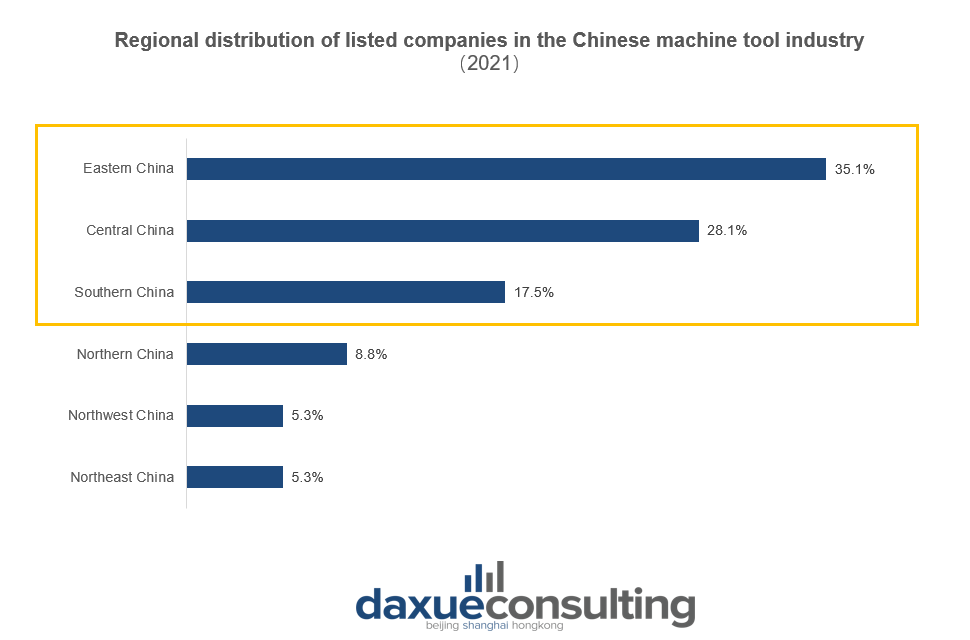
How the Regional Comprehensive Economic Partnership (RCEP) impacted the foreign trade of Made-in-China machine tools
On January 1, 2022, one year after the formal signing of the Regional Comprehensive Economic Partnership (RCEP) on November 15, 2020, RCEP came into effect for six ASEAN member countries, including Singapore, Thailand, Vietnam, Brunei, Laos, and Cambodia, as well as China, Japan, New Zealand, and Australia.
The agreement offers three options to member countries: zero tariffs, 95% tariff reduction, and gradual tariff dismantling, with annual decreases ranging from 0.1 to 1%. The reduction and cancellation of tariffs covered raw materials of machine tools, CNC machine tools, as well as hydraulic and pneumatic components.
Japan and South Korea vaunt mature and high-tech manufacturing industries that dominate the imports of precision machinery, fine chemicals, and CNC machine tools among Asian countries. Undoubtedly, Chinese enterprises will benefit from the removal of tariffs on some CNC machine tools, auto parts, hydraulic parts, and pneumatic components imported from Japan. Taking a further step, the RCEP could help the Chinese machine tools market cut dependence on the US, hence reducing the negative impacts of the trade war. For example, when China imports CNC machine tools from non-member countries like the United States, the tariff can reach 34%. In contrast, Japan as an RCEP member country, only levies a 5% tariff for products of the same quality and precision.
Reasons behind the dominance of foreign manufacturers in the Chinese CNC machine tools market
High-end CNC machine tools rely heavily on imports due to the high technical barriers. The domestic localisation rate of medium- and low-end products is over 65%, while the localisation rate of high-end CNC machine tools is only 6%. According to ChinaIRN, the average price of imported CNC machine tools reached 1.75 million RMB per set in 2021, and the export price of machine tools during the same period was just 100 thousand RMB. In 2021, the CNC rate of China’s metalworking machine tools reached 36.21%, with a year-on-year growth of 11.2%, whereas in Europe, the United States, and other developed countries, the CNC rate has surpassed over 70%.
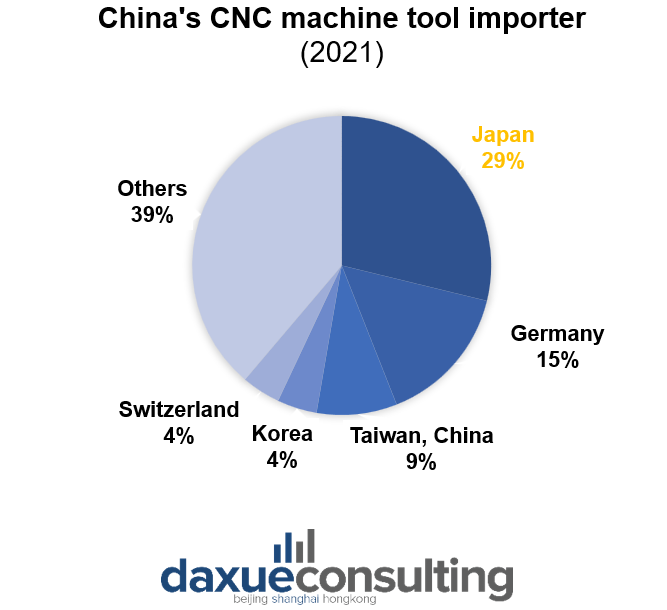
Although the domestic R&D of CNC machine tools has witnessed rapid growth in the past 10 years, there is still a large gap between advanced technology application and manufacturing technology compared to developed countries like Germany and Japan. Especially in terms of accuracy, Foreign advanced horizontal positioning accuracy reached 0.015/1,000mm and 0.003~0.007mm in repeat positioning accuracy. However, the positioning accuracy of domestic CNC machine tools is only 0.025/1,000mm, and the repeat positioning accuracy is 0.01~0.015mm.
On the other hand, domestic CNC machine tools have a relatively higher failure rate than foreign products and much lower durability. The average mean time between failure (MTBF) of foreign machine tools is more than 5,000 hours. However, the MTBF of Chinese CNC machine tools has just improved from 600 hours to 2,000 hours. The most severe issue regarding all reported failures of Chinese CNC machine tools is the leaking of oil, liquid, and gas.
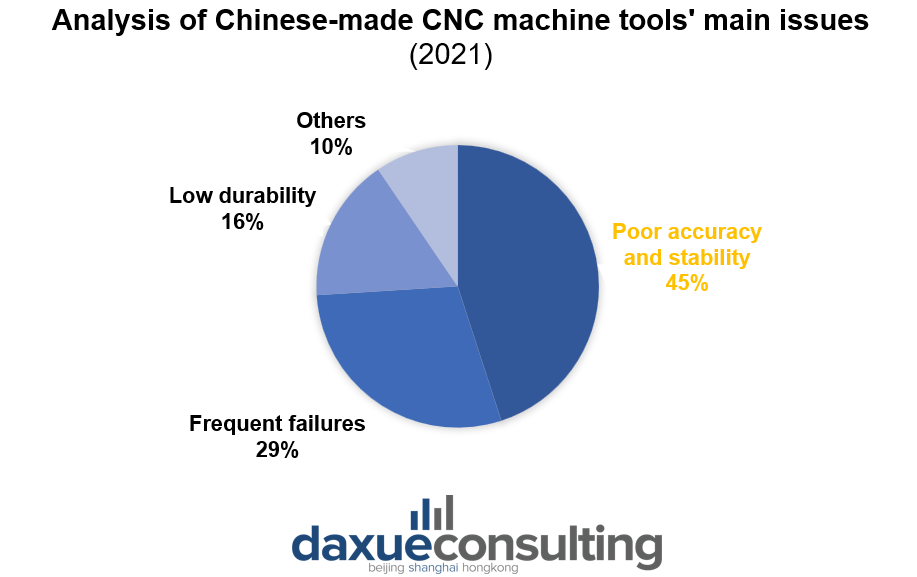
Barriers to developing CNC machine tools
The high-end rolling components market is dominated by brands from Germany, Japan, and Taiwan (China), including THK, NSK, BOSCH REXROTH and PMI. Nevertheless, domestic businesses boast competitive advantage in the mid- and high-end markets. The domestic company primarily concentrated on the low-end market because of technical barriers and the ability to manufacture core components.
Core components
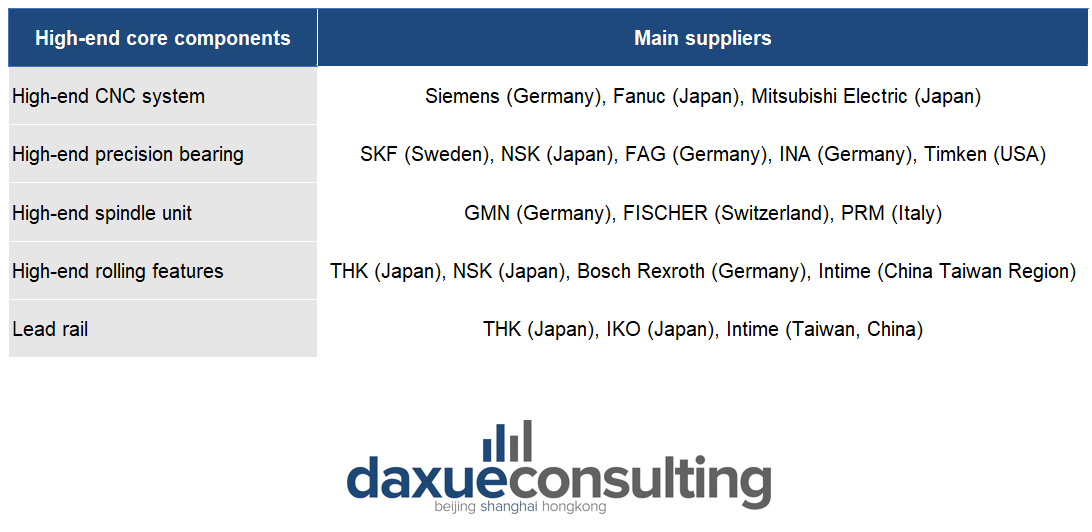
Manufacturing high-end rolling components is one of the most significant barriers to producing numerical control machine tools domestically. Rolling functional parts products mainly include ball screws, rolling linear guide rails, ball splines, ball guide sleeves, linear moving parts, coordinate tables and other parts. High-end rolling components offer high efficiency, low energy dissipation, accuracy, and steadiness to CNC machine tools.
On the other hand, the technology of producing high-end precision bearings has also restricted the development of domestic CNC machine tools. High-end bearings boast outstanding operation and load capacity, long life, high reliability, low vibration noise and friction, and other excellent performance. The accuracy of rolling bearings is generally divided into five levels: P0, P6, P5, P4 and P2, and CNC machine tools usually require P4 and superior ultra-precision bearings. At present, more than 70% of the global bearing market share is monopolised by Japan NSK, Sweden SKF, Germany FAG and America Timken. Quality, production processes, , and versatility of use of high-end bearings are the main reasons for the gap between Chinese high-end precision bearings and overseas counterparts.
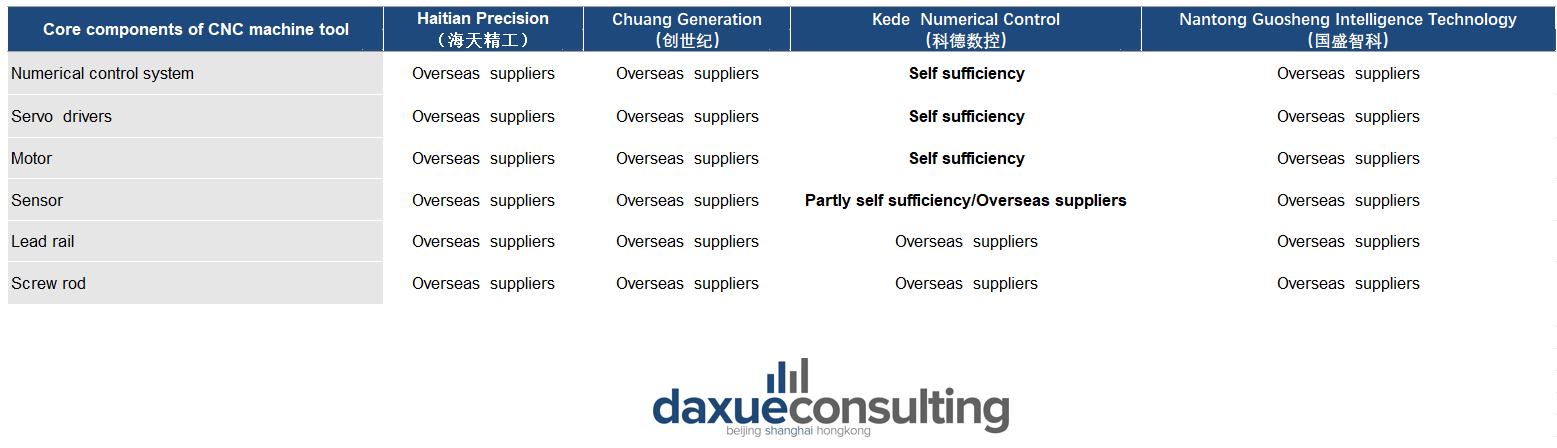
High-end CNC system
The CNC industry plays a significant role in determining critical factors of the performance, function, durability, and cost of machine tool equipment. With economical price and economy of scale, domestic enterprises account for more than 95% of the low-end CNC industry in China. However, when it comes to high-end CNC machine tools, over 90% of supporting CNC system relies on imports. Lastly, regarding the medium-end CNC industry, foreign brands still account for more than 70% of the market. Currently, Siemens, Fanuc and Mitsubishi dominate the mid-to-high-end market of CNC systems in China. Nevertheless, Kede Numerical Control (科德数控) has lately successfully managed to manufacture a high-end CNC system, thereby breaking the long dominance of foreign brands in the Chinese high-end machine tool industry.
China’s efforts on self-sufficiency and cutting dependence on imports
China has already started its journey to self-sufficiency. For this purpose, the Chinese government launched the so-called “Made in China 2025”, a 10-year comprehensive strategic plan aimed to reduce the country’s dependence on foreign technology imports.
The document “Made in China 2025” sets a roadmap for enabling China to move up the value chain and master the development of accurate, high-speed, efficient CNC machine tools, essential manufacturing equipment and integrated manufacturing systems. Moreover, this document aims to accelerate the research and development of cutting-edge technologies and equipment, such as high-end CNC machine tools and precision components before 2025.
In August 2021, as a result of China-US trade war, the Chinese government was forced to further pick up the pace to cut dependence on US high-tech imports. In addition, in order to build a complete ecosystem and industry chain that could support the R&D of homegrown CNC machine tools manufacturers, the Party committee of the State-owned Assets Supervision and Administration Commission of the State Council held a meeting, emphasizing the importance of upgrading the whole domestic CNC machine tools industry chain, as well as encouraging state-owned enterprises to actively integrate themselves into the national system for basic research, application, and innovation to develop China’s own high-end CNC machine tools.
What to know about China’s machine tool market
- China has the largest machine tool market in the world, with the output value of machine tools ranking first in the world. China is also the biggest high-tech CNC machine tools consumer.
- Chinese enterprises will benefit from the RCEP’s removal or cancellation of tariffs on some CNC machine tools and components imported from member countries.
- Chinese high-end CNC machine tools development is restricted by high-end precision bearings, rolling components, and supporting CNC systems. Foreign brands dominate the middle-end and high-end CNC machine tools market in China.
- China’s central government is determined to create a conducive ground for the rise of the CNC machine tools industry in China, breaking the monopoly of foreign brands.